Bruce Anderson
UNL Extension Forage Specialist
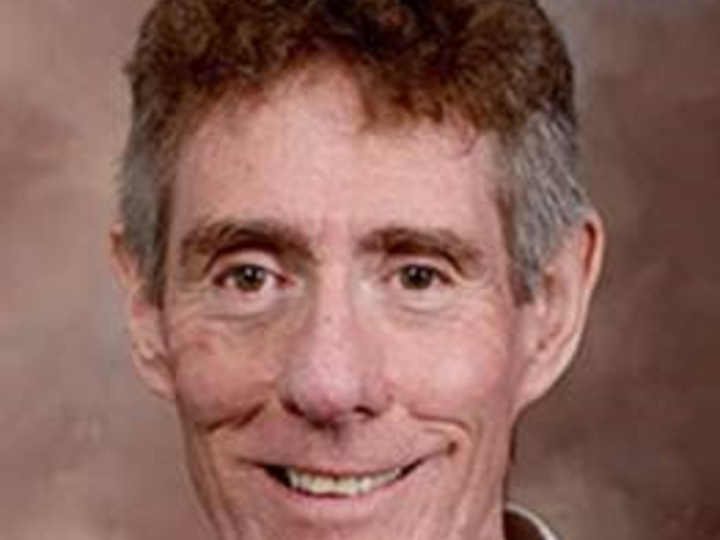
Many dairy diets contain 40% or more corn silage. Most other components of the ration are determined by the quality of this silage so starting with high-quality silage can greatly affect eventual ration cost and milk production. Harvest at the optimal stage of maturity will maximize yield of digestible nutrients and provide the correct moisture content for proper ensiling.
Upright oxygen limiting solos | 50-60 |
Upright concrete stave silos | 62-67 |
Bag silos | 60-70 |
Horizontal bunker silos | 65-70 |
Silage harvested too wet often seeps and can result in an undesirable sour fermentation. Harvesting too dry, though, can produce large fermentation losses and reduced digestibility due to heat damage. Corn kernel characteristics like black layer or kernel milk line can serve as guidelines for determining when to harvest but hybrids differ significantly in whole-plant moisture content at the same kernel development stage. Measure actual whole-plant moisture to insure proper fermentation.
Length of chop affects packing of silage as well as silage intake and conversion. Traditionally, dairy silage has been cut at 3/8 to ½ inch to maintain good digestive health of the cow. When silage processors are used to increase starch digestion and breakup cob pieces, theoretical length of cut often can be increased to ¾ inch.
Add an appropriate silage inoculant during the chopping process to stimulate more rapid fermentation and pH decline, resulting in less fermentation loss and/or better aerobic stability and longer bunk life. Recent advances in inoculant development have created products with better, more consistent benefits than earlier generation inoculants. However, to be effective, inoculants must be stored, mixed, and applied correctly and at the appropriate rate.
An area of silage management that often is overlooked is the process of filling and packing, especially bunker silos. Fill the silo quickly to reduce the time forage is exposed to air, thus reducing respiration and oxidative losses. When filling bunkers use progressive wedges. Never distribute chopped forage in layers thicker than 6 inches, otherwise air will be trapped inside and increase losses. One of the most common mistakes when filling bunker silos is inadequate weight of packing equipment relative to the rate at which silage is delivered to the silo. To ensure adequate packing, take the delivery rate (tons silage per hour) times 800 to equal the minimum packing weight required (in pounds). For example, if 30 tons are delivered per hour, a minimum of 24,000 pounds of packing tractors is needed (30 x 800). This will help achieve a target packing density of at least 45 pounds fresh weight per cubic foot.
Finally, cover the pile with plastic and secure the plastic with tires, low quality chopped forage, or some other weighting material to protect the cover from puncture and reduce moving air under the plastic. This can reduce spoilage in the top 3+ feet by 50% or more.